Sectors of Bright Bars
Let’s Start Work
Together
Please feel free to contact us. We will get back to you with 1-2 business days. Or just call us now.
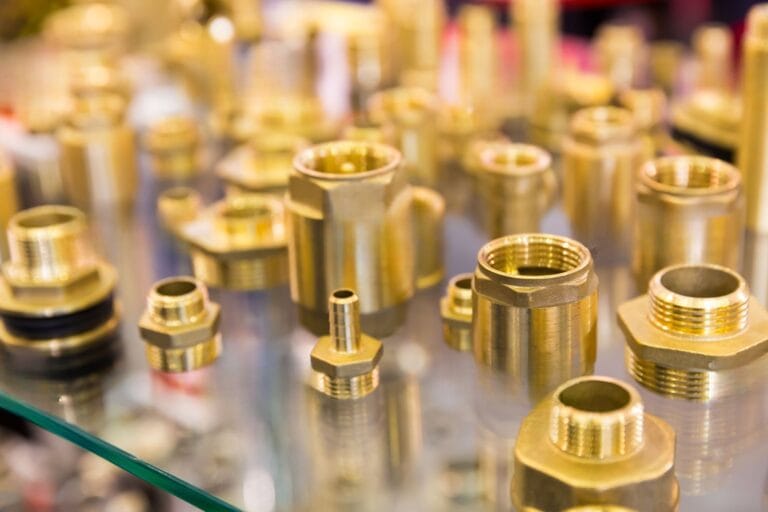
Application and Uses of bright steel bars in Hydraulic Component Industry
Common Metals used for manufacturing Hydraulic Fittings, Adapters and Ferrules include coated carbon steel , if heavy duty pressures are controlled at an affordable cost.
Stainless Steel is used where the internal media or the environment is highly corrosive.
Two general fitting categories are based on geometry — straights and shapes. Straights are typically machined from cold drawn, hexagonal, or sometimes round bar stock. Shapes are typically forged or brazed.
Because forgings are single-piece construction, they have no potential leak paths, which can occur with a two-piece brazed fitting. Also, forged fittings are normally stronger because they are not limited by the strength of the brazed joint. This added strength typically produces longer life and higher-pressure ratings than brazed fittings.
Some manufacturers prefer brazed fittings because of the large number of configurations that can be made with little investment in capital equipment. As a result, brazed fittings are usually offered at a lower price to the user.
Material selection considerations-The raw material for Hydraulic fittings must have adequate strength and corrosion resistance to safely handle the high pressures characteristic of hydraulic systems. In addition, the fitting material must resist rust and corrosion from the different media inside and outside of the vessel. Other selection factors include cost and outside environmental conditions.
Generally, metal fittings are used in most hydraulic systems due to their high pressure ratings. Plastics have naturally higher resistance to corrosion than metals but have lower strength and durability, making them less suitable for hydraulic systems.
Carbon steel is durable, strong, and has a high resistance to heat, with a temperature range of –54°C to 260°C. An alloy of iron and carbon, it is typically alloyed with other metals to improve strength, toughness, and other properties.
External protective coatings such as electroplated cadmium, zinc, and zinc phosphate are applied to carbon steel fittings to extend their service life in corrosive environments. However, in the past decade, cadmium is no longer accepted by most industries due to environmental considerations. Cadmium and zinc corrode sacrificially, protecting the steel substrate from normal atmospheric rusting due to the common presence of oxygen, moisture, and acidic gases. However, they are rapidly attacked by many fluids — including those containing acidic hydrogen, reactive fluorine, chlorine, bromine, iodine, and nitrogen. Zinc-nickel external coating provides enhanced carbon steel protection in ASTM B117 salt spray testing and in fertilizer (urea) applications. Nowadays Trivalent Zinc coating is more popular due to the longet life under salt spray conditions and highly environmental friendly attitude observed by the factories in general.
Stainless steel is strong and has excellent chemical and corrosion resistance. Its temperature range is –254°C to 649°C. Stainless steel is an alloy of steel that contains more than 10.5% chromium. It has the strength and durability of steel while also providing excellent corrosion resistance, making it the most suitable fitting material for hydraulic applications where the fluid or surrounding environment is corrosive. Stainless steel’s toughness is significantly better than carbon steel’s at low temperature.However, many applications require its corrosion resistance — oil, gas, and offshore equipment; chemical processing; food manufacturing; medical and instrumentation; agricultural fertilizer; and marine applications.